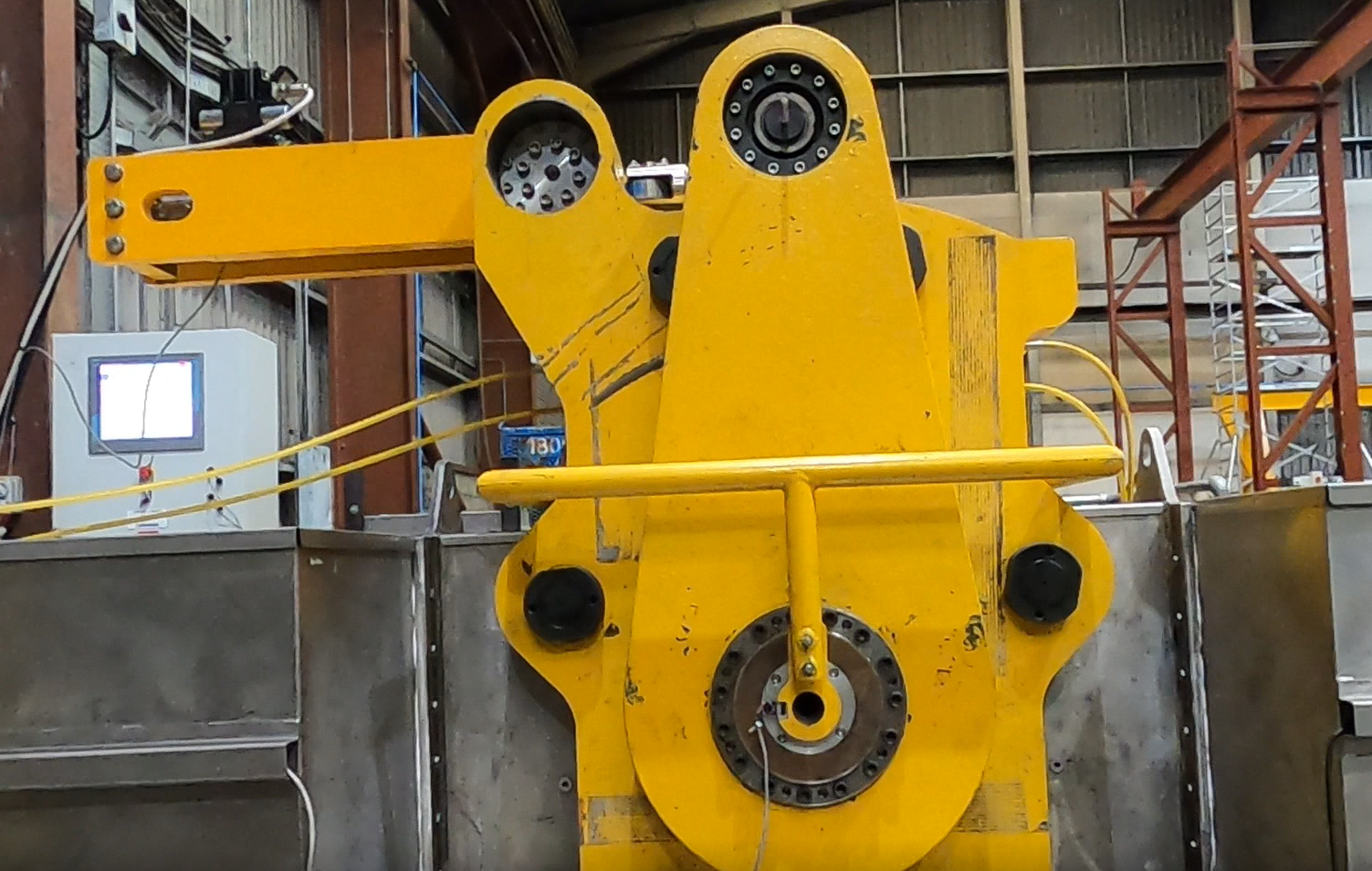
The floating offshore wind industry brings great opportunity and new challenges for mooring systems in comparison to previous experiences in oil and gas. In semi-submersible hull design, we see motions which are considerably different from the much larger structures found in oil and gas and that in turn leads to a more severe environment for bearings. The potential for wear is much greater and the range of loads far wider. In TLPs we see need for simplification of tether connections capable of high pre-loads and significant motions.
Flintstone has invested a substantial amount of time and money understanding how best to optimise bearing design and the team have developed a test rig which can simulate the wide range of loads, angular movements, and combinations of both. Test rig results are combined with non-linear finite element analysis.
The results obtained are influencing the design of connectors and tensioning equipment being developed by Flintstone. The combination of long life and lowest cost is critical for the successful development of this nascent industry.